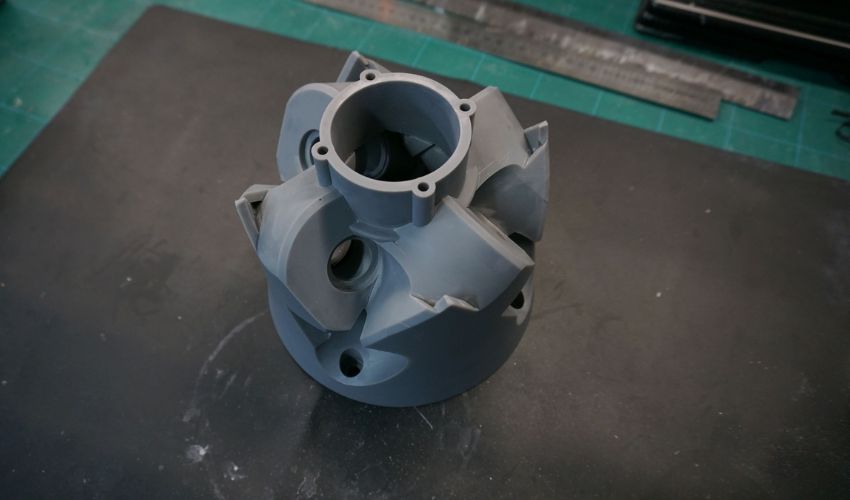
Additive manufacturing has reached such a level of maturity that it now enables the creation of all kinds of parts with advanced materials, ensuring effective and cost-efficient solutions even in the most extreme environments, from the sky to space and the depths of the ocean. A striking example of this technological revolution is Velettrica, an Italian startup that has utilized 3D printing to develop key components for the functional prototype of the SAIL-POD 25 sailboat engine. To learn more and discover how the use of cutting-edge technologies, such as 3D printing and biomimetic design, is opening new frontiers in « sustainable sailing, » we spoke with Velettrica’s founder, Roberto Baffigo.
3DN: Can you introduce yourself and tell us about your connection to 3D printing?
Hello, my name is Roberto Baffigo. I was born in 1972 in Rome and throughout my life, I have always engaged in sports—rowing, sailing, mountain biking, skiing, and now fin swimming. I studied physics, which sparked my curiosity and desire to experiment. My connection to 3D printing comes from the world of jewelry: the shift from manual prototyping to digital was a true revolution that exploded with the availability of increasingly reliable and cost-effective printing techniques. Subsequently, 3D printing allowed me to rapidly test all the inventions contained in Velettrica’s innovative propeller.
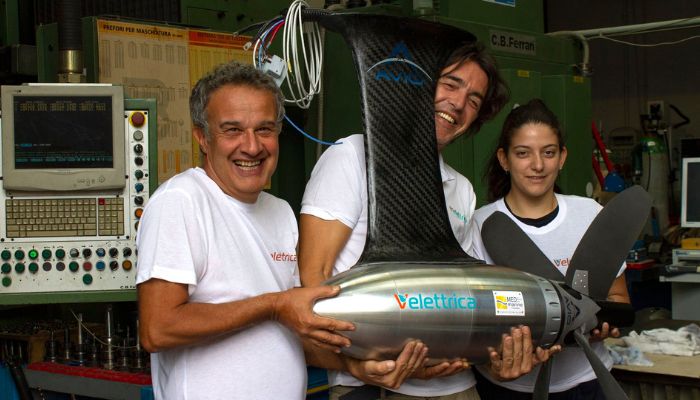
3DN: How did Velettrica come about and what is its mission?
Velettrica was founded in 2021 from the dream of exploring sailing with minimal impact—a concept that matured during sailing vacations with my wife Chiara and our children, Stella and Pietro Noè. I have always dreamed of traveling with them in harmony with nature. I wanted to make the sailboat even more environmentally friendly by using an electric motor, not only for propulsion but also to generate energy when powered by the wind. The motor developed for the Velettrica project is called the SAIL-POD 25.
Velettrica’s mission is clear: to develop energy-efficient propulsion systems primarily powered by renewable sources to reduce sea pollution. The core of Velettrica’s innovation lies in a multifunctional propeller equipped with an electronic control system, designed with a biomimetic approach inspired by the whale shark’s fins. When not in use, this propeller folds into a flower-like shape, minimizing water resistance and optimizing the energy efficiency of the propulsion system.
3DN: Can you tell us more about the SAIL-POD 25 engine? How has additive manufacturing been utilized in its creation?
We used 3D printing for several components of the SAIL-POD 25. In some cases, the final parts were produced directly, while in other cases, rapid prototyping was used to create molds or cores for the composite material. The SAIL-POD 25 is a highly efficient propulsion and electric charging system for sailboats, featuring a foldable and variable-pitch propeller. It is easy to install, takes up minimal space inside the boat, is pollution-free, and requires no maintenance. It produces no noise, vibration, or heat.
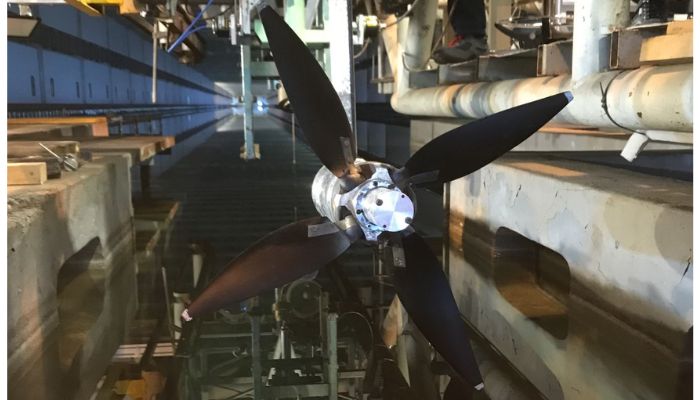
Designed in Italy by Velettrica, 3DiTALY printed some of the components for a functional prototype of the engine using a combination of materials and printing technologies. The Formlabs SLS Fuse 1 printer and Nylon 12 powder were used to create the core of the propeller blades. This thermoplastic offers high tensile strength and environmental stability, making it particularly suitable for producing complex assemblies and durable components with minimal water absorption. The first prototype of the propeller hub for dry testing, due to its complex shape, was produced using the Formlabs SLA Form 3L printer and Grey resin to achieve a high level of detail, a smooth and matte surface finish, and optimal mechanical properties. Finally, « special » mechanical parts are made from Inconel or aluminum using DMLS technology, while the fin mold is made from an HDT photopolymer using SLS technology.
3DN: Why did Velettrica choose 3D printing?
For many components, it was a necessary choice; given the « novel » and complex nature of the patented mechanisms, it would have been impossible or excessively costly to produce them using traditional technologies.
Moreover, 3D printing offers multiple advantages, such as the ability to produce rapid prototypes in less than 24 hours; cost reductions of up to 90% compared to machining; the production of complex parts such as propellers and turbine blades for underwater equipment; the use of advanced materials with desirable properties such as fire resistance, reduced toxic emissions, and corrosion resistance; and, finally, on-demand production, which allows designers to obtain parts exactly when and where they are needed, thus reducing storage costs, the risk of overproduction, and environmental impact, while promoting efficiency and sustainability.
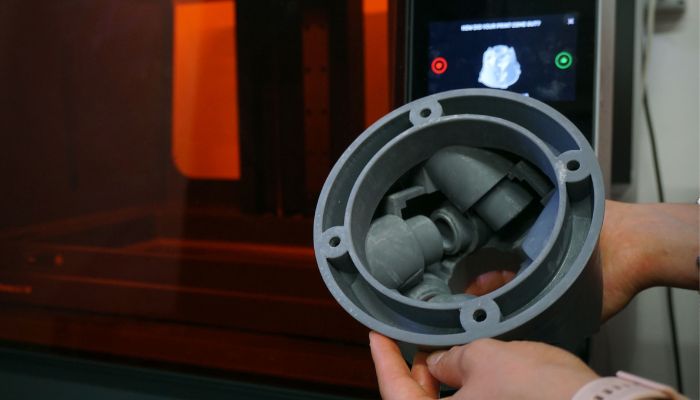
3DN: How do you see the role of additive manufacturing in the maritime sector?
The naval sector, particularly in the field of electric propulsion, is often characterized by or benefits from custom or semi-custom production. Additive manufacturing, as we’ve discussed, offers significant freedom by reducing the costs of custom-made components. Moreover, the sustainability advantages include both the savings in raw materials and energy during production compared to other techniques, and the ease of recycling the materials used at the end of the component’s life, particularly for thermoplastics. Finally, polymer materials are much closer to providing anti-fouling protection compared to metals, which allows, for example in propellers, for reduced chemical dispersion into the environment and maintains efficiency with the resulting energy savings.
Source: 3dnatives